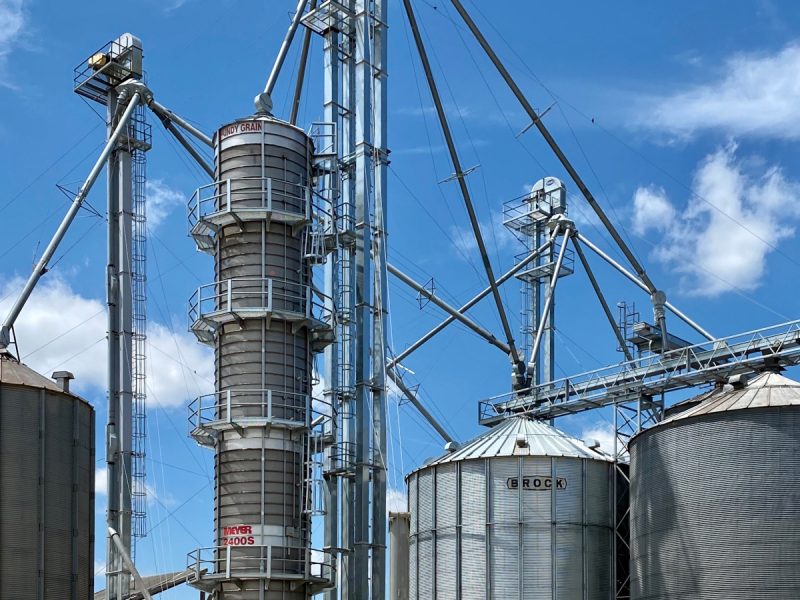
How we helped Mundy Inc rebuild after a devastating storm.
In late 2018 the Mundy Elevator suffered severe damage due to high winds damaging several legs, conveyors, bins and drier. With the help of our manufactures representative and millwright, MHES was asked to redesign their plant to improve existing flow conditions. During the initial sight visit in early January of 2019 we took several measurements to start the process of putting all the pieces back together.
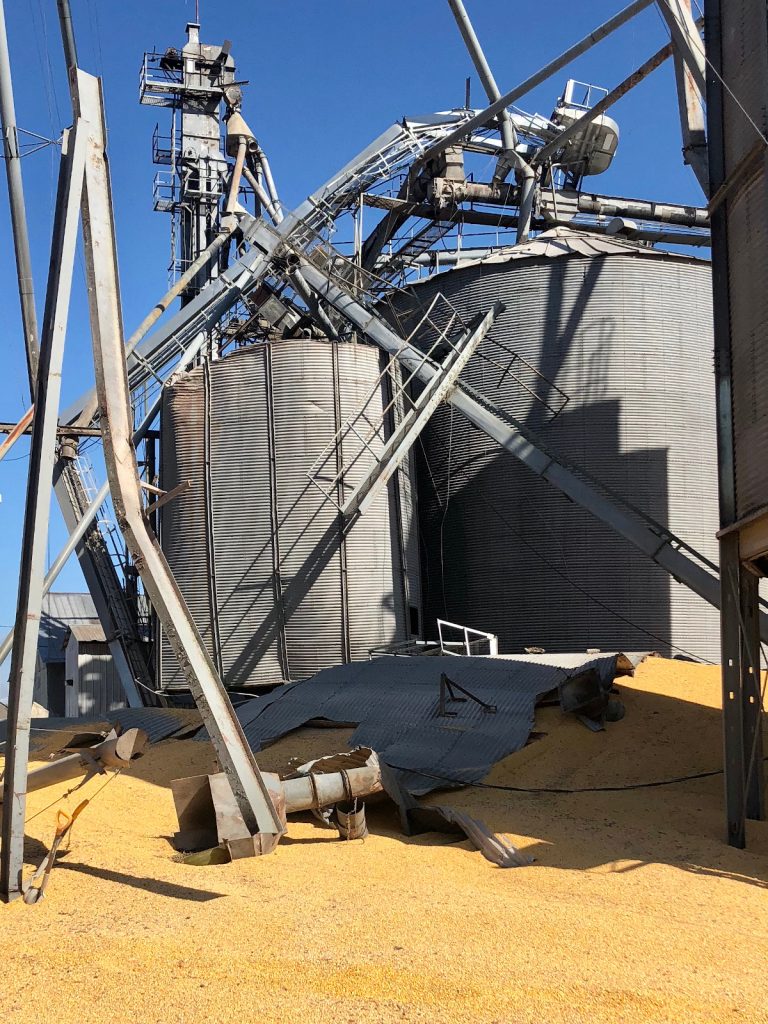
With these measurements MHES put a layout drawing together presenting several options to the manager for improving their overall flow to accomplish their goals. We then created a detailed bill of material in a formal quotation explaining all the benefits of MHES equipment. The damaged equipment was replaced with commercial grade galvanized bucket elevators and conveyors.
Structurally we were concerned with the integrity of the existing bins requiring all new catwalks and support towers. In addition, this improvement will allow for the bins to be replaced in the future without excessive cost related to this installation.
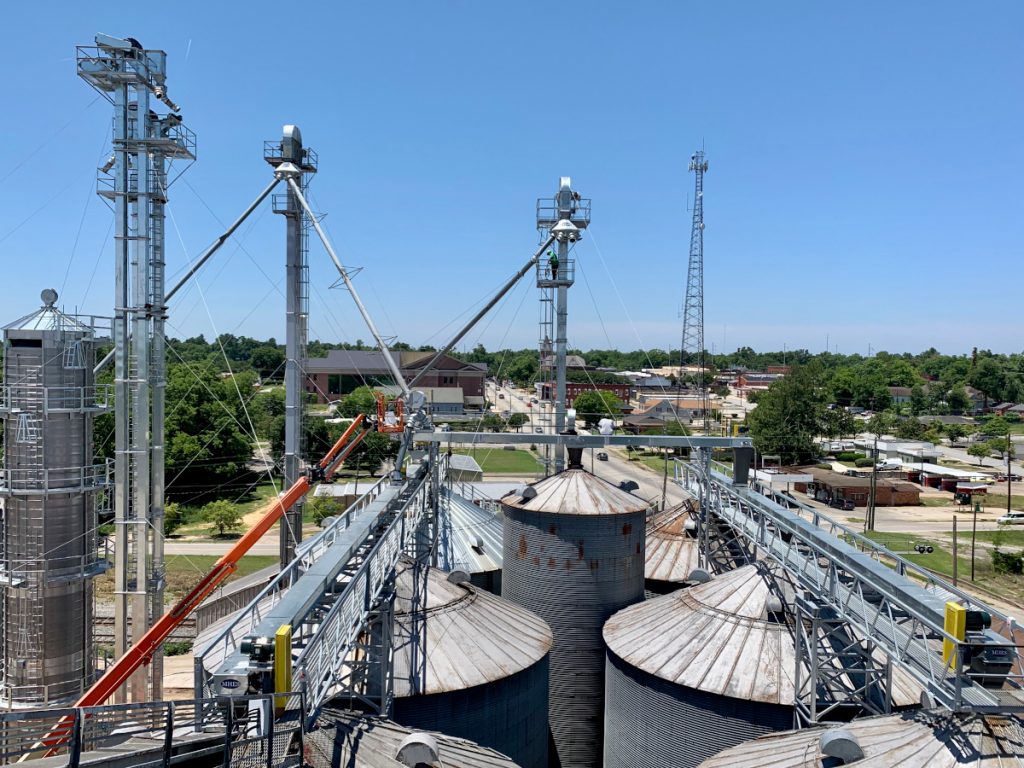
After managing their first successful harvest later that fall, owner Jay Mundy said “He was very happy with the equipment and the job that we did.” We were able to improve many of his flow issues with quality commercial grade equipment. His only complaint was that they were not used to legs that run so quietly and smoothly that he accidently left it running for several days not realizing that it was on.
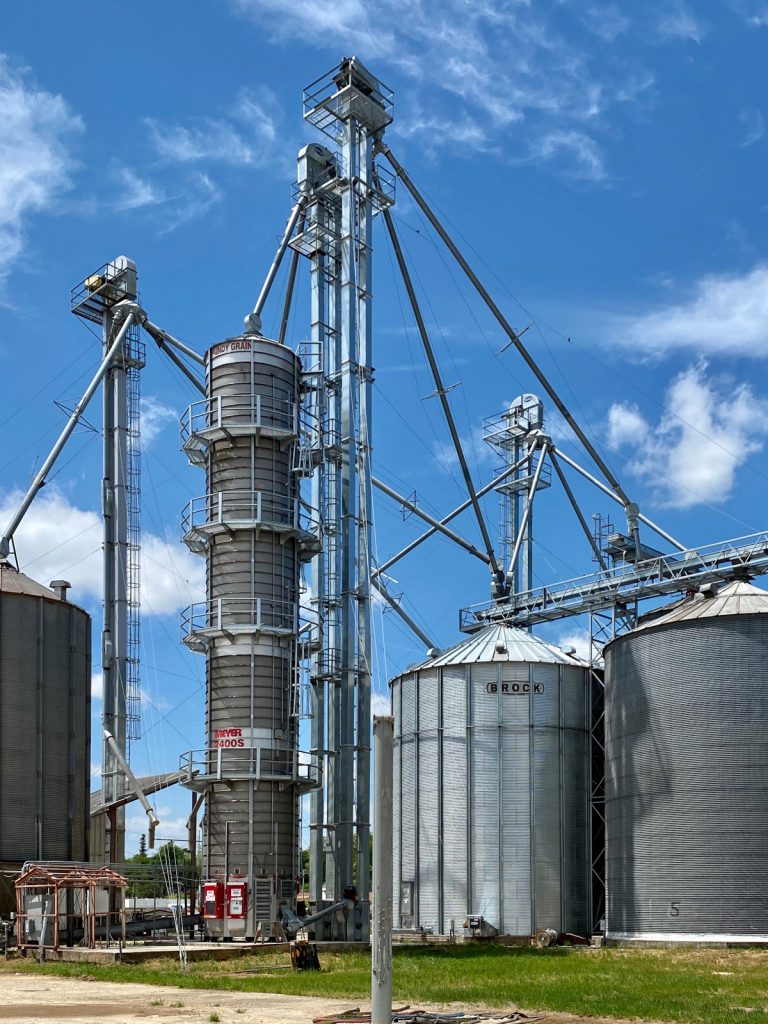
This project was the perfect example of the process that we take at MHES. Working with our dealers and customers to achieve their goals. Utilizing our buying power to provide all of the equipment and accessories at very competitive pricing levels. Coordinating layout drawings with the concrete and installation contractors. A good plan starts with a good drawing. Our knowledge of our equipment and our understanding what makes things cost allows us to better explain things to customize our equipment for their specific needs.